How Three Verticals in the Flexible Packaging Industry Help Brand Owners
Film Grade
When choosing a film, Charter Next Generation considered selecting either a white or clear PE film. The company decided on a white PE film, as it would be a more difficult to pass the APR’s test due to its additional additives. If the structure could pass on white PE film, then the company estimated that clear PE film would likely be a success, too. Charter Next Generation’s GreenArrow GAP-222.21 HBWTST film was selected for the study.
1. Film Grade
2. Cold Seal Grade
3.Cold Seal Coat Deposition
Many verticals within the flexible packaging industry have pledged that 100% of their packaging will soon be recyclable, reusable or compostable, according to the 2022 Ellen MacArthur Global Commitment Report. For brand owners especially, meeting this commitment is critical to their company’s success. However, because regulations and certifications that relate to packaging’s end of life continue to evolve, it can be challenging to ensure the packaging always meets them and ultimately accomplishes the pledge.
THE SITUATION
A cold seal PE film packaging case study featuring American Packaging Corporation, Bostik and Charter Next Generation
When conducting the latest guideline reviews on flexible PE recycling streams, How2Recycle determined that the extent to which cold seal adhesive coatings influence the recycling streams was unclear. To help the industry better understand the impact of cold seal adhesive coatings, How2Recycle requested that experts test materials via the Association of Plastic Recyclers (APR)’s Critical Guidance Testing for PE Film and Plastic Packaging. In addition, How2Recycle stated that all brand owners using cold seal in their PE packaging had one year to validate that their packaging met recyclability standards. If unable to do so, all existing PE cold seal packaging that once had received Store Drop-off recycling status would be nullified, and the Store Drop-off labels would need to be removed from that packaging. Additionally, brand owners would be unable to obtain Store Drop-off certification for any new PE cold seal packaging until testing was completed.
Because many brand owners use PE cold seal packaging, there became urgent need in the market to determine how cold seals impacted the recycling process.
THE PROBLEM
In particular, within North America, How2Recycle®, an entity that standardizes disposal instructions on packaging labels for the public, annually publishes recycling guidelines for packaging using flexible polyethylene (PE), which is the only U.S.-recyclable film to date. These guidelines aim at providing clear and consistent message on packaging material recycling status.
They detail what kinds of packaging structures can be recycled in various recycling streams and indicate which part of the structures require additional testing and pre-qualification letters. Brand owners then use these pre-qualification letters when their final packages are submitted to How2Recycle in order to obtain Store Drop-off certification if applicable. Having this certification means their packaging can have a label on it informing consumers they can bring the packaging to participating stores with PE collection bins. For brand owners, this helps build brand loyalty, making it easy for consumers to know exactly what to do with the packaging and how they can reduce their environmental impact.
Upon learning this news, flexible film converter American Packaging Corporation reached out to its adhesive supplier, Bostik, Inc. Together, they partnered with Charter Next Generation, a leader in PE films.
Given that cold seal is an inherent part of the film that gets recycled, they knew the entire structure needed to be tested – not only the cold seal. Additionally, they understood the importance in working together to meet the due date, prevent nullification and eliminate future brand owner issues in obtaining the certification.
First, American Packaging Corporation, Bostik and Charter Next Generation needed to decide which packaging structure to submit for testing. Click through below to learn the criteria that was considered:
Determining The Solution
Cold Seal Grade
When choosing a cold seal grade, Bostik recommended its most difficult grade in terms of its composition. This grade would have the highest likelihood to gel during the blown film portion of the APR’s test. Gels can be detrimental when trying to blow a PE film from recycled material as gels can cause holes in the blown film and make the material collapse. If the cold seal grade with highest likelihood to gel could pass recycling standards, then the group theorized that other compositional grades less likely to cause issues would pass, too. Ultimately, Bostik’s Turbo-Seal® 1961 was selected for the study.
Cold Seal Coat Deposition
Coat Weight: When deciding how the cold seal should be applied to the film, American Packaging Corporation recommended a heavy coat weight of 3.5 lb/ream. This is because the company wanted to test the material with as much adhesive on it as possible to truly gain an understanding of cold seal’s impact and increase the difficulty in passing the APR’s test. If a low coat weight was used, the amount of adhesive would be less, thereby making any impact be less as well and the test easier to pass.
Pattern: When deciding on the pattern in which the cold seal would be applied, all companies agreed that a pattern with a high level of film coverage should be used so that all lower coverage applications would be covered as well. Similar to coat weight, lower coverage applications contain less adhesive and minimize the effect of cold seal on the film’s recyclability. The cold seal coverage was approximately 60% of the film.
After agreeing on design criteria, Charter Next Generation and Bostik supplied American Packaging Corporation with the raw materials to create a converted test structure.
American Packaging Corporation created two rolls for testing; the first roll was designated as Innovation Film, which was the cold seal-coated PE film; the second roll was designated as Control Film, which was uncoated PE film. The samples were sent to Plastics Forming Enterprises (PFE), an APR-approved test lab to conduct Critical Guidance Protocol for PE Films testing based on the APR test protocol.
Implementing The Solution
PFE’s results showed the Innovation Film was not detrimental to the recycling process per the APR’s test protocol.
CERTIFICATIONS RECIEVED
This means Charter Next Generation PE film utilizing Bostik cold seal could be recycled in Store Drop-off streams. As a result, How2Recycle granted a pre-qualification letter that brand owners could use when submitting their packaging; Bostik’s cold seal could continue to be used in cold-seal coated PE structures, and it supported efforts to improve recycling stream effectiveness.
Collaboratively, American Packaging Corporation, Bostik and Charter Next Generation were able to determine with test data that Bostik’s cold seal coated on Charter Next Generation’s PE film is pre-qualified for Store Drop-off recycling. This is beneficial to brand owners, as it allows them to have confidence when developing a recyclable PE cold seal structure that their packaging will:
Value to the brand owner
Meet APR standards for recyclability
Not negatively impact the PE recycling stream
Be easy for consumers to recycle, and therefore increase their likelihood of purchasing it
1.
2.
3.
Furthermore, the structure tested was intentionally designed to be a difficult structure to pass the test in order to cover all other structures, whether that be the PE film grade, Bostik cold seal grade or cold seal deposition.
Without collaboration, Bostik would have been unable to submit the cold seal to PFE; Charter Next Generation would not know if their film was compatible for recyclable cold seal applications, and American Packaging Corporation would lose their pre-qualification letters for cold seal PE packaging applications. Ultimately, brand owners would be at risk for losing Store Drop-off eligibility for their packaging.
This cross-vertical collaboration enabled all companies to become experts in the design criteria for creating a recyclable PE structure for cold seal applications and helped brand owners more easily expand their recyclable product lines and develop more sustainable packages for the market.
©2023 Bostik, Inc. All Rights Reserved
All information contained herein is believed to be accurate as of the date of publication, is provided “as-is” and is subject to change without notice. To review our full U.S. Legal Disclaimer, visit: https://bostik.com/us/en_US/privacy-policy/legal-disclaimer
Want to get started with American Packaging Corporation, Bostik and Charter Next Generation?
Contact our technical team members today!
www.americanpackaging.com
www.bostik.com/us
www.cnginc.com
TM
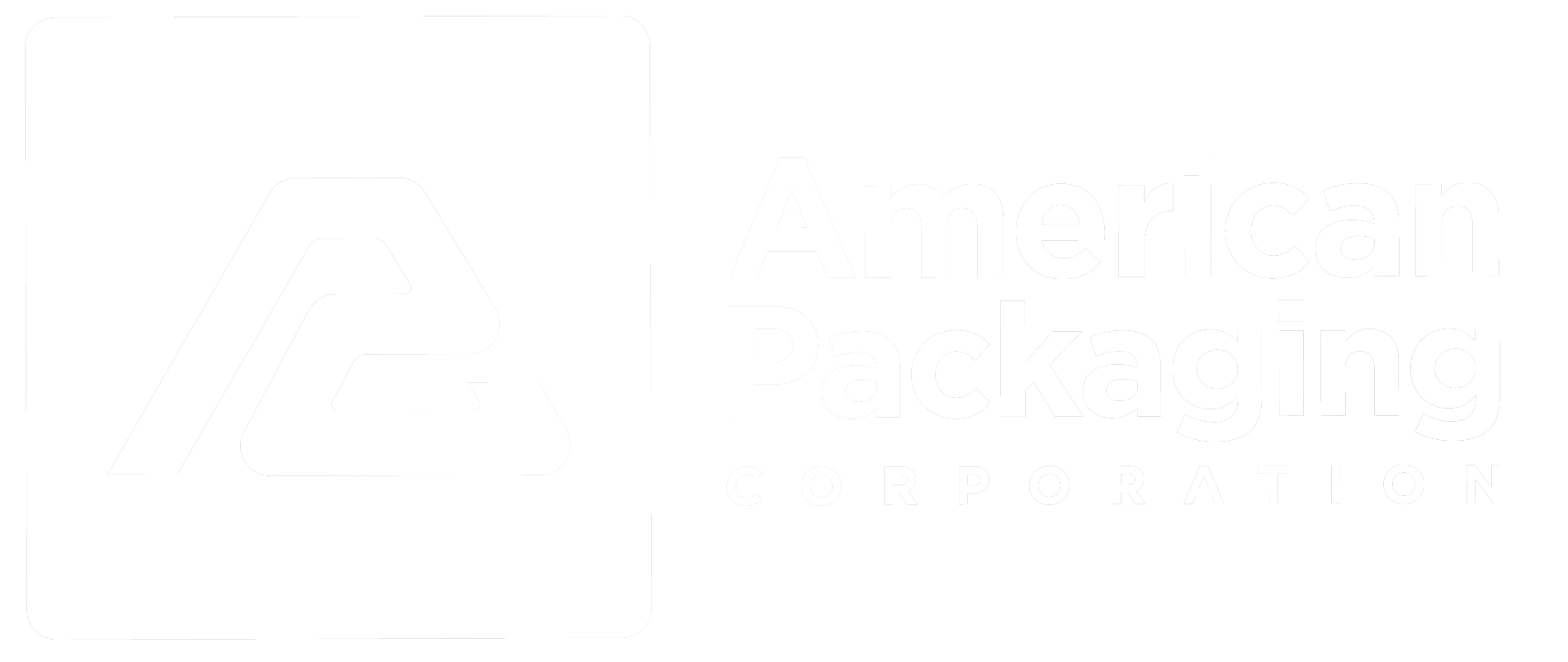