While you may be using solvent-based acrylic or rubber-based, hot melt pressure sensitive adhesives (PSAs) in your graphics or tapes, there are limitations with both options. Fortunately, 100% solid, UV acrylic PSAs can overcome them, providing you with a more sustainable solution without sacrificing performance levels or processing speeds.
However, we understand switching adhesive technologies can seem daunting. This guide aims to make it simple, letting you know what to expect based on your current equipment and technology as well as providing coating and processing tips.
How to Effectively - and Easily - Incorporate UV Acrylic PSAs in Your Production Lines
©2023 Bostik, Inc. All Rights Reserved
All information contained herein is believed to be accurate as of the date of publication, is provided “as-is” and is subject to change without notice. To review our full U.S. Legal Disclaimer, visit: https://bostik.com/us/en_US/privacy-policy/legal-disclaimer
Ready to incorporate UV acrylic PSAs into your production?
Talk to a Bostik expert today!
Solvent-based acrylic and UV acrylic PSAs are based on the same polymer chemistry, but different equipment is required for processing. This is because UV acrylics contain 100% solids; therefore, they don’t need ovens to evaporate off solvents.
This means you’ll need to invest in a hot melt PSA coater, which is designed for PSA technologies that are comprised of 100% solids. It includes:
If Currently Using Solvent-Based, Acrylic PSAs
UV lights
Drum unloader
Buffer tank
Feed lines
Slot-die coating head
If Currently Using Solvent-Based, Acrylic PSAs
If Currently Using Rubber-Based Hot Melt PSAs
Best Practices for Coating UV Acrylic PSAs
Best Practices for Processing UV Acrylic PSAs
If Currently
Using
Solvent-Based,
Acrylic PSAs
If Currently
Using
Rubber-Based Hot Melt PSAs
Switching to UV acrylic PSAs will require upfront investment in new equipment.
UV lights to cure the adhesive
Drum unloader to push adhesive out of drum to feed buffer tank
Buffer tank to heat the adhesive and continuously pump it to the slot die
Feed lines between drum unloader, buffer tank and slot die coating head
Slot-die coating head (optional) that can coat facestock or release liner applied to the adhesive
While UV acrylic PSAs and rubber-based hot melt PSAs are based on different chemistries, they require similar equipment. This is because they are both hot melt technologies that are comprised of 100% solids.
You already have a hot melt PSA coater; so, to run UV acrylic PSAs, you may only need to incorporate these components:
You also don’t even need to fully switch!
You can use both!
Switching to UV acrylic PSAs will require minimal capital investment.
If Currently Using Rubber-Based
Hot Melt PSAs
We recommend running the hot melt coating line with a drum unloader and heated buffer tank.
The combination of equipment will allow continuous production without stopping to change out a drum. The heated buffer tank pumps the adhesive to the slot die and the drum unloader replenishes the adhesive in the buffer tank.
Why?
UV Curable Hot Melt Adhesive Curing Line
Decrease energy usage by approximately 85% (no natural gas required, only electricity)*
Increase line speeds by at least five times, especially at thick coat weights*
Reduce plant’s equipment footprint
Unlike solvent equipment, it does not require drying ovens or thermal oxidizers and ventilation systems to account for solvent or volatile organic compound (VOC) evaporation; therefore, it will take up less facility space as a result and allow you to:
Take special care to avoid cross-contamination of the adhesives in your coating equipment. This may occur because the two chemistries are not compatible with each other, remaining homogenous.
The separate delivery system (drum unloader) will help to reduce cross-contamination likelihood.
Have dedicated transfer lines and buffer tanks to avoid mixing hot melts and UV acrylics, especially given that these adhesives can be processed at different temperatures.
If you plan to run UV acrylic and rubber-based, hot melt PSAs on the same coating line...
Since UV acrylic PSAs and rubber-based, hot melt PSAs have different chemistries, a separate delivery system (drum loader) is recommended.
Tip
Manufacture products with both chemistries to expand product offerings and enter new markets such as building construction and automotive
Improve performance levels by providing high shear and UV and chemical resistance
Continue to process materials without using solvents to improve carbon footprint
Increase process speeds to reduce energy usage while achieving similar performance to solvent acrylic PSAs
A separate delivery system can help you:
Developing a routine maintenance program for UV light components
UV light is utilized to cure the adhesive when coating UV acrylic PSAs. Therefore, we recommend that you develop standard processes for the following:
Best Practices for Coating
UV Acrylic PSAs
Determine the best operating conditions for curing UV products
Achieve consistent process conditions for each coating production run
Standardizing these processes will allow you to:
From initial product trials to commercial production coating lines, the following should be measured and recorded throughout processing:
Process #1: Measuring and Documenting UV Coating System Parameters
UV production coating line in use
Bulb type
Bulb hours
Number of bulbs used for cure
Input power to the lamp
Radiant energy density or dose (mJ/cm2) of UVA, UVB, and UVC light
Irradiance or intensity (mW/cm2) of UVA, UVB, and UVC light
Light distance from the curing surface (or focus of the light)
Processing temperatures of components such as chill roll, drum unloader, buffer tank, heated lines, and slot die
Line speed
Date of last scheduled maintenance on UV system
Changes in UV light intensity or UV dose while maintaining the same speed may require investigation or maintenance for the UV system. This can occur for various situational reasons, such as buildup on the lights.
A radiometer is required to measure radiant energy density and irradiance. UV systems should be designed with clearance for a radiometer to pass underneath the light while being attached to silicone release liner. In systems with multiple lamps, a specialized radiometer can be used to measure the energy density and irradiance of each lamp independently.
Important Notes
Recording and monitoring each of the above variables that impact adhesive cure will help ensure consistent product quality and performance.
Logging and checking these coating line parameters will also provide information on your UV system efficiencies over time.
WHY?
UV acrylic PSA performance should correlate with the variables measured above to help ensure consistent product performance. Similar to measuring the oven temperatures for a solvent-based adhesive for consistent performance, you should ensure the amount of UV light is the same each time so the adhesive provides consistent performance. Use standard PSA tests to determine the curing window to achieve the desired performance.
In the case where a product is moved from one coating line to another, the process data can be a starting point for the product transfer to the new UV hot melt coating line.
Process #2: Performance Testing for UV Light
Curing Conditions
Quartz window cleaning
Reflector inspection and cleaning
UV bulb inspection and cleaning
UV lamp replacement schedule/trigger
Regularly scheduled UV light system maintenance is critical to maintain control over a coating process. This ensures environmental factors in your facility, such as dust, are not impacting your coater over time. UV light maintenance includes:
Process #3: Routine Maintenance Program for
UV Light Components
Startup time to reach the desired quality levels
Poor performing products due to improper maintenance
Waste by understanding your operating window
By implementing these standard programs, you can decrease:
Additionally, you can increase throughput by cleaning lamps for consistent UV light output.
UV acrylic PSA curing involves a combination of coat weight, UV dose and irradiance. Processing conditions highlighted in the table below offer a starting point for you with each of our product offerings. Final processing conditions should correlate to adhesive performance testing, and an operating window for optimum cure and performance should be developed for your specific coating line.
Best Practices for Processing
UV Acrylic PSAs
Bostik’s technical service team is here to support you throughout the process of testing and troubleshooting. We’ll work with you to provide suggestions on customized adhesive formulations for your specific needs. Further, we can help you address issues on-site to ensure you have a seamless transition.
How Bostik Can Help You Get Started with UV Acrylic PSAs
*Based on internal testing
Testing performance of adhesive correlated with UV light curing conditions
Measuring and documenting UV coating system parameters
Heated Drum Unloader
110-150°C
Heated Tank
110-150°C
Heated Slot Die Coater
110-150°C
Release Liner or Substrate
Shielding to Protect Individuals From UV Light
Exhaust of Ozone and Cooling Air
Blowers Provide Air Flow to Maintain Bulb Temperature
To Laminator or Windup Station
Bulb is a medium pressure mercury bulb
UVC dose is measured with a EIT PowerPuck II (250-260 nm).
The UVC dose and irradiance (or intensity) is a recommended starting point to be used as a guide. Performance testing should be used to determine best
UVC dose for the application.
1.
2.
3.
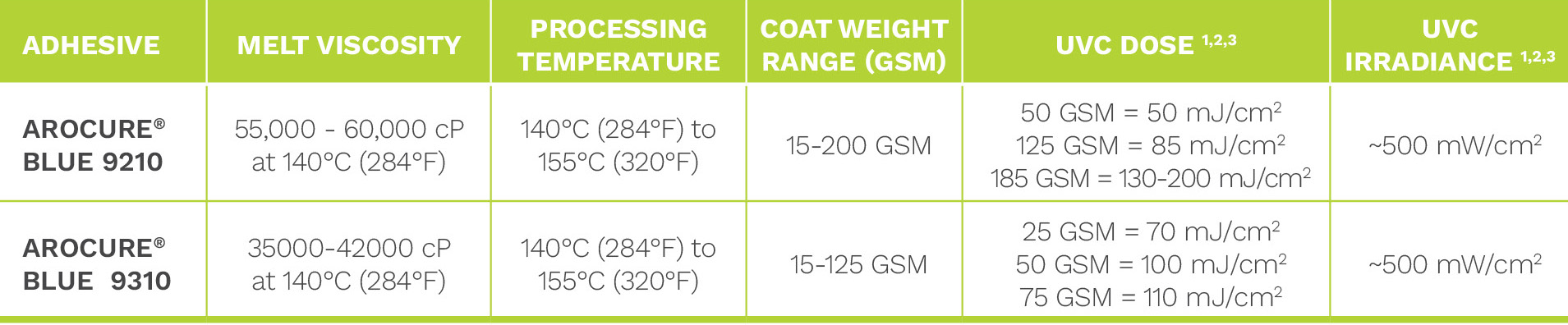