There are three basic approaches to recycling PV modules: mechanical, chemical, and thermal. Currently, mechanical recycling processes are the benchmark approach. In mechanical recycling, modules are shredded, crushed, and milled to extract individual materials like silicon, glass, and silver, which can be processed and refined for reuse.
There are both advantages and disadvantages to this prevailing recycling technique. Its cost and ability to scale make it attractive for large volumes of solar modules. The benefits and the limitations of mechanical recycling were apparent in the study's examination of LCI data from Germany-based Reiling Glas Recycling GmbH. Reiling's new facility, with an annual capacity of 50,000 tons, is an example of a mature mechanical recycling approach optimized for cost and low energy consumption. However, Reiling's well-established recycling process does not allow for the recovery of valuable silicon and silver.
Though mechanical recycling remains the benchmark approach, several innovative technologies are in the pilot stage and show the potential to lower the energy needed to recycle and bolster the total amount and purity of materials recovered, including silver and silicon. Some recyclers, for example, are now testing chemical processes to remove materials from solar modules, including using solvents like water vapor and limonene that dissolve module components and allow for the extraction of silicon, silver, and other metals. Other recycling techniques rely on thermal measures, such as pyrolysis, incineration, or polymer melting.
Researchers examined companies pursuing innovative recycling techniques, including the German company Flaxres GmbH. Founded in 2017, Flaxres combines mechanical and thermal techniques, including applying high-intensity light pulses to heat silicon and enable delamination. Flaxres's pilot recycling line is also mobile, meaning that it can be transported to project sites where large volumes of solar modules need to be recycled.
U.S.-based thin-film module manufacturer First Solar has a well-established approach to recycling its modules. One of the largest module manufacturers in the world, First Solar has recycling plants located alongside its manufacturing facilities in the U.S., Malaysia, Vietnam, and Germany. Taken together, the facilities can treat 50,000 tons annually and recover more than 90 percent of all the materials in the recycled modules.
Another indication of interest in solar module recycling is the growing volume of patent applications and scientific research. The study identified 456 patents related to recycling PV components and 569 scientific papers and publications. Almost 80 percent of the patents are associated with recycling processes for silicon modules, cell metals, polymers, glass, and devices. Not surprisingly, most patent filings have occurred in countries with large manufacturing capacity and big installation markets, such as China, the U.S., South Korea, Japan, and Europe. For the most part, universities, module makers, and research organizations are behind the patent filings, although some recyclers and waste treatment companies have also applied for patent protection.
Universities and research institutions are also the leading publishers of academic papers focused on PV recycling, albeit often in conjunction with module manufacturers, equipment suppliers, and recyclers. There is wide geographic diversity among the authors publishing papers and articles. While U.S. authors have the most publications, followed by Italy and China, researchers from developing countries and emerging PV markets like Ghana, South Africa, and Mexico have also produced scientific papers.
Key Findings From EPRI's PV Recycling Survey
PREVIOUS
NEXT
Mechanical Recycling Remains Dominant
New Technologies Hold the Promise of Improved Recycling Quality
olumes of solar modules need to be recycled.
First Solar Has a Mature Recycling Process for Thin-film Modules
Steep Increase in Patent and Research Activity
PREVIOUS
NEXT
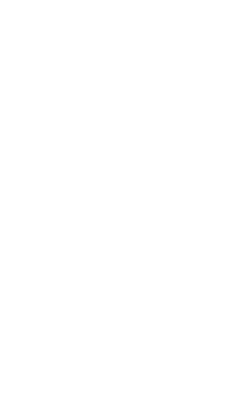