studio visits
studio visits
Situated in the scenic and historic Le Locle, Zenith’s Manufacture is about a one-hour drive from the center of Neuchâtel, Switzerland. Alongside La Chaux-de-Fonds, its geographical twin, and the hometown of pioneering modern architect, Le Corbusier, both towns are classified as UNESCO World Heritage Sites as part of its Watchmaking Town Planning initiative. Arriving at the manufacture, even the exteriors of Zenith’s main entrance are unmissable – designed by contemporary artist Felipe Pantone, the building’s façade has been clad in a tarpaulin canvas and doused in a “pixelized” spectrum of colors. Just the journey to the manufacture itself already sets the tone for Zenith’s central themes, as well as its ongoing mission to preserve heritage while paving the way for innovation and modernity.
Experience how the Maison harks
to its past in its journey to innovation and modernity.
Exploring the otherworldly artworks of the Brooklyn-based painter and sculptor.
Le Locle, Switzerland
zenith-watches.com
Yok & Sheryo
Did you have similar styles before you met?
Sheryo: My style is really wonky and really imperfect because I like imperfection. My lines were super wavy when I drew and his was kind of straighter. He would draw a straight line. Try to get really straight on the wall and spray can and I'll be like, "Yo. I'm just going to do it wonky." Because it's easier. It's done by hand.
Yok: I had a cleaner style. A bit more, I don't know, it was a bit more work and trouble to make the cleaner style and then I met Sheryo and she had this loose, wobbly, wonky style and I was envious of it and kind of adapted into that. It’s kind of like that new airbrush work that we've been doing. I kind of just embrace the looseness and the wonkiness of it in the conception.
The Maison is one of the few manufactures that has a close relationship with the country’s tourism office, with dedicated tours and programs that the public can take part in. Stretching 9000㎡ today, the headquarters was initially constructed in 1865 by founder Georges Favre-Jacot, who “had the vision to gather all the different crafts under the same roof,” as Julien Tornare, the Maison’s CEO mentioned in a previous interview with Hypebeast. This is evident in the large monochromatic print displayed near the site’s reception and boutique area, which features the manufacture's entire reproduction of its factory buildings from 1865. Today, the site has kept the bright and spacious environments that the founder had intended, along with many of its historical charms intact.
I was doing reverse painted acrylic polymer peel paintings for a long time, and those were hyper-detailed and all super hard-edged and super meticulous. It got to a point with that where I guess around like 2012, I wanted to start doing something more visceral and more painterly and less sort of slick.
What is the process of creating a menu?
“Our job is to create the bridge between the past, present, and the future.”
- Romain Marietta
cj hendry
“Its ongoing mission to preserve heritage while paving the way for innovation and modernity.”
Sheryo: Not as much as we like to. Now, we’re very busy with studio work and traveling to different locations in Southeast Asia.
Yok: Yeah, we’re busy finding places to do installations. It’s our new thing. We also travel often to learn niche handicrafts. We get stoked about going to places like Indonesia and spend months learning how to do Batik and making other local artisan works.
What was the process for designing the Borough location?
Throughout the history of Zenith, the luxury watchmaker has earned its reputation for its expertise in producing reliable, and highly precise movements. Every component of a Zenith calibre, including its molds and stamping tools, remains to be produced in-house at its Le Locle manufacture. Even when it comes to decorating these components, Romain Mazzilli, our tour guide, and Zenith’s brand experience manager explains, “We try to do everything in-house to preserve the know-how. If you sub-let this, within a year or two, you’ll lose the know-how.” He also elaborates that this sense of responsibility to upkeep the brand’s technologies is something that every staff at Zenith resonates with.
One of Zenith’s most eminent crown jewels is the El Primero calibre. First introduced in 1969, the calibre was the first-ever automatic high-frequency integrated chronograph movement in history. As Mazzilli puts it, the Maison’s most renowned calibre was deemed a “crazy” idea at its initiation. With an astounding rate of 36,600 VpH, it was considered the “UFO” movement of its time. In addition, Luc Diener, a movement engineer from Zenith’s R&D department even describes the process of developing a watch movement akin to playing Tetris. .
The fact that the legendary El Primero movement continues to live and thrive in today’s world is a consequence of Charles Vermot and his sacred attic. At the time of the quartz crisis, where mechanical watches were largely replaced by cheaper electronic alternatives, the Maison was under the management of a U.S. company, named Zenith Radio Corporation. This led to Zenith ceasing all productions of mechanical movements, hence the order to dispose of all associated technical plans and tools. As one of the original watchmakers who worked on the El Primero movement back in the ‘60s, Vermot had secretly stowed everything away inside the manufacture’s attic.
An excerpt from a letter Vermot had sent to the then-owner of the company reads, “I’m not against progress, this is how the world is, in the sense that it always harks back to the past. You are wrong to consider halting the production of automatic mechanical chronographs. I am convinced that one day, your company will benefit from the fads and fashions of yesteryear.” With hopes that one day the El Primero would make its return, the attic remained as Vermot’s secret and was sealed and walled up for years. It wasn’t until the Maison’s rebirth in the ‘80s, Vermot finally revealed his secret after Rolex expressed an interest to modernize its Daytona models using Zenith’s El Primero calibre.
Are you both still doing that now?
Today, visitors of the manufacture are able to get a taste of Vermot’s secret mission by ascending the very-same winding spiral stairway to the Le Grenier Charles Vermot, which literally translates to the Charles Vermot Attic. The moment you step foot inside the attic, you’re welcomed into a space that feels as if it has frozen in time – just the way Vermot had left it. From cams, stamps and cutting tools to small machines, everything is kept in an organized library, accompanied by an antique and musty scent of aged wood. Without Vermot, Zenith’s comeback may not even have been possible.
To seek references from the past while paving a way to build and innovate for the future is a pervasive message that is constantly reminded at Zenith's headquarters. A prominent example of this spirit is evident in our sit-down session with Zenith’s Chief Product Officer, Romain Marietta, and Laurence Bodenmann, Head of Heritage. “Our job is to create the bridge between the past, present, and the future,” Marietta tells Hypebeast, “Aside from developing new products, it's important to discuss the past and find ways that we could create bridges between history and what we're doing now.”
The duo presented a physical showcase of the Pilot’s timeline during our session, covering pieces from the model’s initial form as a professional aircraft timekeeper, to its varying iterations as a wristwatch that lived through the Golden Era of Aviation, and the modern resurgence of the aviator aesthetic. As highlighted by Marietta, the fact that the Maison can completely revamp the Pilot watch is because they had already trademarked the name decades ago. “Having the name Pilot and the right to put it on the dial is a statement. It's something that the other watch brands cannot have or do,” says Marietta. To which, Bodenmann also adds, “We have what it takes to make it evolve again. But for our 2023 Pilot, it's a whole new thing, because we can escape from the vintage image that others couldn't, as they need a design that reminds people they're still pilot watches.”
Yok: We would look at our drawings and imagine how it would be great if they were worlds that you could go inside, touch and move around. That's where the installation inspiration came from, I guess.
Sheryo: It was kind of natural, really, a progression from 2D to 3D. Yeah.
What about installations are you both most fascinated by?
Yok: We’re working on an immersive installation at the Paddle 8 auction house at the Lower East Side of New York City. We’re creating this nine-foot wooden sculpture of a middle finger with Donald Trump’s tombstone on top.
Sheryo: It’s this pretty big basement spot. We are making sculptures as well as creating the upholstery and benches. It has a really dingy and dark vibe. It’s kind of a lounge room setting. It’s going to launch this coming fall season.
What are you both working on right now?
By : Zoe Leung
As we navigate around the manufacture’s numerous workshops, it’s unmistakable just how much the Maison’s histories and heritage still permeate the site. Modern machinery, such as highly-efficient 3-axis and 5-axis CNC machines dominate the halls today. Some of the manufacture’s much older analog machines are still kept on-site for archival and research purposes, or as historic exhibits decked across stairway landings and hallways.
With an annual average of producing approximately 25,000 watches, the Zenith manufacture today is fully integrated and mostly self-sufficient. Offering a rather compact catalog of time-tellers, the Maison’s core collection now comprises Defy, Chronomaster, Elite, Icons, along with the recently relaunched Pilot. In addition, Zenith also has a Revival concept, where they revisit vintage timepieces from the brand’s archives, which are then bestowed a second life via a modern reinterpretation.
In terms of watch design, Zenith draws inspiration from the past. The Maison’s head of design, Sébastien Gobert tells Hypebeast that he often wears a vintage Zenith 135 to work, mostly to look for historical design influences, but also to prevent the fear of being affected by modern references in the designing process. When it comes to helping the Maison conceptualize the next time-telling offering, Gobert explains that “the best way to design a watch is that you want to be able to recognize it from far away.”
“The best way to design a watch is that you want to be able to recognize it from far away.” - Sébastien Gobert
As the finishing touch to our tour, we are taken to the manufacturer's Watch Clinic. In spite of its name, the clinic isn’t where watch restorations or repairs take place. Reserved for guests and visitors, the space is designed as an interactive workshop where participants can immerse themselves in certain areas of watchmaking.
As part of the experience, Mazzilli, Zenith’s brand experience manager, ran us through the history of watch lumes. Radium powder was widely used since the start of the 1900s, but due to its radioactive nature, it had gradually been phased out by the mid-'60s. It was then replaced by tritium, a not as luminous, but slightly safer alternative. From 1999 onwards, the non-toxic Luminova/ Super-LumiNova (SLN), which was invented by Japanese company Nemoto & Co. has taken over as the gold standard for watch lumes.
Zenith’s LumiNova workshop was first unveiled at Watches & Wonders this year, but this is the first time an official group gets to participate in this workshop on-site. On each portable tabletop workbench is a box of tools, magnifier, UV torch, UV glue, luminescent powder, mixers, alongside hour and minute hands that awaits to be lume-filled. From mixing to application, the process only takes a few minutes, and then another few for the hands to dry and bake in the oven. Once it was done, we were able to affix the hands in a clear case at our preferred time. At the end of the workshop, we each had a pocket-sized case that displayed our very-own hand-lumed hour and minute hands, which we brought home as souvenirs for our tour, and as a reminder of how Zenith upholds its heritage and modern vision with equal importance.
studio visits
studio visits
Throughout the history of Zenith, the luxury watchmaker has earned its reputation for its expertise in producing reliable, and highly precise movements. Every component of a Zenith calibre, including its molds and stamping tools remains to be produced in-house at its Le Locle manufacture. Even when it comes to decorating these components, Romain Mazzilli, our tour guide, and Zenith’s brand experience manager explains, “We try to do everything in-house to preserve the know-how. If you sub-let this, within a year or two, you’ll lose the know-how.” He also elaborates that this sense of responsibility to upkeep the brand’s technologies is something that every staff at Zenith resonates with.
One of Zenith’s most eminent crown jewels is the El Primero calibre. First introduced in 1969, the calibre was the first-ever automatic and high-frequency integrated chronograph movement in history. As Mazzilli puts it, the Maison’s most renowned calibre was deemed a “crazy” idea at its initiation. With an astounding rate of 36,600 VpH, it was considered the “UFO” movement of its time. In addition, Luc Diener, a movement engineer from Zenith’s R&D department even describes the process of developing a watch movement akin to playing Tetris. .
Today, visitors of the manufacture are able to get a taste of Vermot’s secret mission by ascending the very-same winding spiral stairway to the Le Grenier Charles Vermot, which literally translates to the Charles Vermot Attic. The moment you step foot inside the attic, you’re welcomed into a space that feels as if it has frozen in time – just the way Vermot had left it. From cams, stamps and cutting tools to small machines, everything is kept in an organized library, accompanied by an antique and musty scent of aged wood. Without Vermot, Zenith’s comeback may not even have been possible.
To seek references from the past while paving a way to build and innovate for the future is a pervasive message that is constantly reminded at Zenith's headquarters. A prominent example of this spirit is evident in our sit-down session with Zenith’s Chief Product Officer, Romain Marietta, and Laurence Bodenmann, Head of Heritage. “Our job is to create the bridge between the past, present, and the future,” Marietta tells Hypebeast, “Aside from developing new products, it's important to discuss the past and find ways that we could create bridges between history and what we're doing now.”
The duo presented a physical showcase of the Pilot’s timeline during our session, covering pieces from the model’s initial form as a professional aircraft timekeeper, to its varying iterations as a wristwatch that lived through the Golden Era of Aviation, and the modern resurgence of the aviator aesthetic. As highlighted by Marietta, the fact that the Maison can completely revamp the Pilot watch is because they had already trademarked the name decades ago. “Having the name Pilot and the right to put it on the dial is a statement. It's something that the other watch brands cannot have or do,” says Marietta. To which, Bodenmann also adds, “We have what it takes to make it evolve again. But for our 2023 Pilot, it's a whole new thing, because we can escape from the vintage image that others couldn't, as they need a design that reminds people they're still pilot watches.”
As the finishing touch to our tour, we are taken to the manufacturer's Watch Clinic. In spite of its name, the clinic isn’t where watch restorations or repairs take place. Reserved for guests and visitors, the space is designed as an interactive workshop where participants can immerse themselves in certain areas of watchmaking.
As part of the experience, Mazzilli, Zenith’s brand experience manager, ran us through the history of watch lumes. Radium powder was widely used since the start of the 1900s, but due to its radioactive nature, it had gradually been phased out by the mid-'60s. It was then replaced by tritium, a not as luminous, but slightly safer alternative. From 1999 onwards, the non-toxic Luminova/ Super-LumiNova (SLN), which was invented by Japanese company Nemoto & Co. has taken over as the gold standard for watch lumes.
Zenith’s LumiNova workshop was first unveiled at Watches & Wonders this year, but this is the first time an official group gets to participate in this workshop on-site. On each portable tabletop workbench is a box of tools, magnifier, UV torch, UV glue, luminescent powder, mixers, alongside hour and minute hands that awaits to be lume-filled. From mixing to application, the process only takes a few minutes, and then another few for the hands to dry and bake in the oven. Once it was done, we were able to affix the hands in a clear case at our preferred time. At the end of the workshop, we each had a pocket-sized case that displayed our very-own hand-lumed hour and minute hands, which we brought home as souvenirs for our tour, and as a reminder of how Zenith upholds its heritage and modern vision with equal importance.
A Look Inside
Zenith's Manufacture
A Look Inside
Zenith's Manufacture
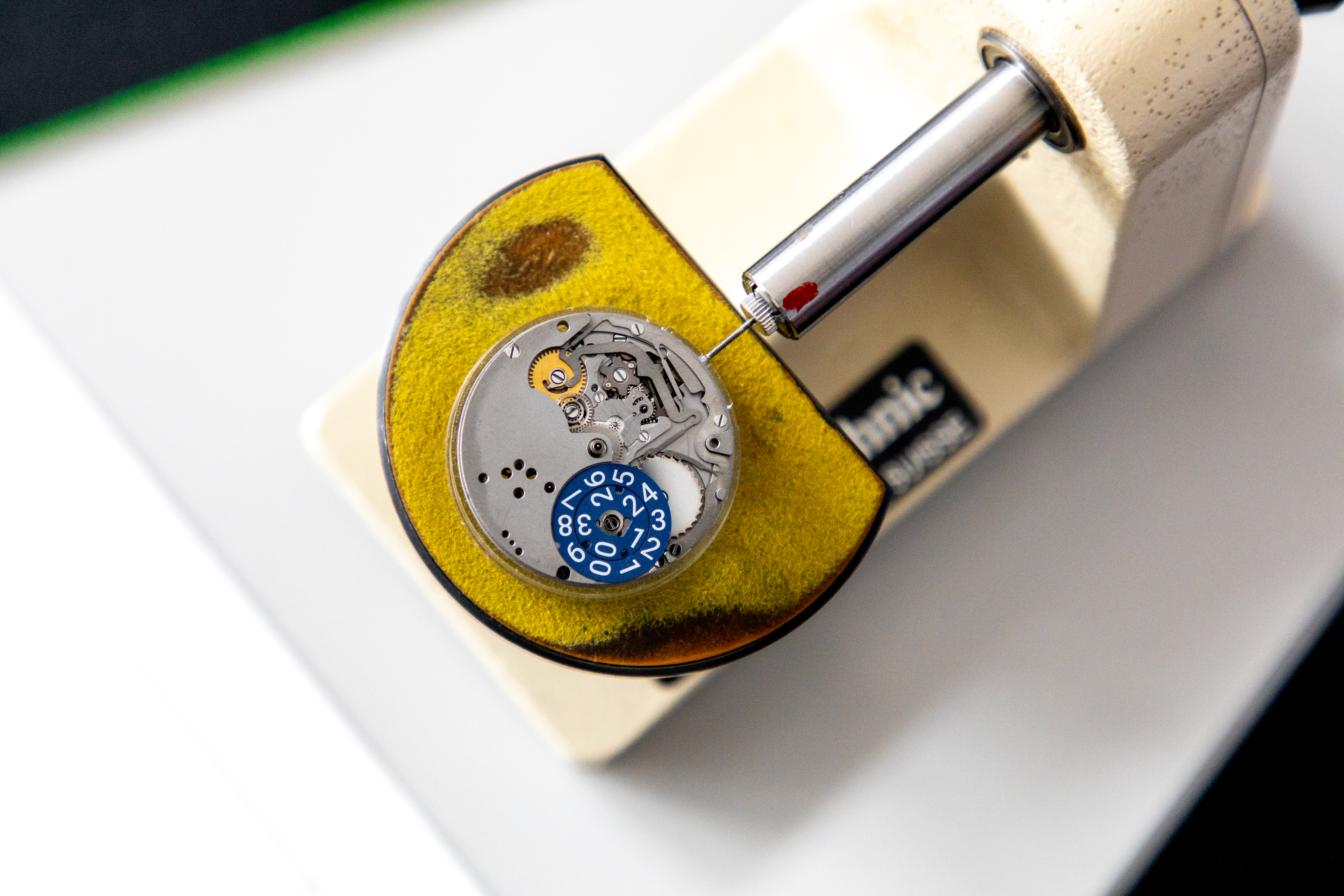