Charting the Course of
Digital Transformation
A Roadmap to Manufacturing Success
How Far Can Manufacturers Go with Digital Transformation?
for surviving in today’s manufacturing landscape. Challenging market conditions have forced market leaders to reconsider established practices to become more resilient in the face of volatility and rapid change. Industrial companies are turning to new digital solutions as they rethink how their physical products are engineered and manufactured.
What is Driving Digital Transformation?
While the value of investment in digital transformation has been proven beyond debate, emerging vulnerabilities have boosted the need for change.
Industrial markets are contending with a widening skills gap and millions of open jobs.
Global companies are facing increasing macroeconomic and cost pressures.
Traditional enterprises are threatened by the rise of digital business models and competitors who are farther along in their digital transformation journey.
X Marks the Spot: How Digital Transformation is Benefitting Manufacturing Companies
nearly half of industrial companies around the world experience measurable benefits from turning data into actionable insights and fully realizing business outcomes.
92% of industrial companies are executing digital transformation initiatives with goals of achieving:
How to Plot an Enterprise-Wide Digital Transformation Journey
it's about redefining an organization’s strategy and mindset, empowering employees to embrace change, and utilizing technology to accelerate the value creation for clients and stakeholders.
A sound and effective transformation strategy is based on the People, Process, Technology (PPT) framework, with three pillars summarizing how the organizational elements interact:
These three components must be balanced and coordinated for a successful enterprise-wide transformation. They must also be supported by a corporate change management program that is focused on:
Leadership
Employee
experience
Augmented
workforce
Engagement
culture
Enhanced
collaboration
Innovation
and creativity
Lifelong
learning
Talent
retention
Navigating Around Pilot Purgatory Pitfalls
it can be a complicated, time-consuming process. According to Frost & Sullivan, pilot purgatory (failure to straightforwardly scale pilot projects) and scale purgatory (failure to capitalize on pilots and promptly capture the desired impact at scale) can affect nearly 65% of industrial companies embarking on their digital transformation journeys.
Boosting Productivity by 5 to 20% with PTC’s Manufacturing Solutions
by connecting and integrating the digital and physical worlds to enable real-time, priority-driven, closed-loop problem solving. This can propel your digital transformation journey by leveraging its enterprise-level capabilities as it identifies priority bottlenecks, analyzes root causes, then improves and scales processes to be more efficient moving forward.
Check out the latest Frost and Sullivan Report
Discovery 1: Speed Loss
The previous OEE indicated one hour of speed loss due to minor stops. After using DPM, the team realized that speed loss accounted for four hours of lost time per week – three more than they previously thought.
01
Speed loss
Discovery 2: Changeover
Changeover time was the same in both scenarios, but the team hypothesizes that it is correlated with the high amount of speed loss. They plan to investigate further.
02
changeover
Discovery 3: Minor Stops
The team’s previous OEE indicated only one hour of performance loss due to minor stops. The team is surprised to learn that minor stops actually cause 5 hours of loss every week.
03
Minor stops
Discovery 4: Unaccounted Time
Unaccounted time is the difference between planned production hours and effective time. NewCo has 88 hours of planned production per week, including overtime. It also has 57 hours of effective time per week, leaving 21 hours of lost production time. The team has attributed 17 of those hours using DPM’s loss buckets, which include unplanned downtime, planned downtime, changeovers, and other types of time loss. The remaining four hours are unaccounted for, meaning they were not factored anywhere but still lost on a weekly basis. Since traditional OEE systems are still focused on ratios and percentages, they have no way to identify such time gaps.
04
Unaccounted time
01
speed loss
02
changeover
03
Minor stops
04
Unaccounted time
Learn more about how PTC’s manufacturing solutions can help propel your organization’s digital transformation journey and generate impactful, quantifiable benefits to help you stand out against competition.
to find out how organizations are achieving digital maturity and what it means to succeed in Industry 4.0.
PTC’s solutions for manufacturing can help avoid the pitfalls of pilot and scale purgatory
Digital transformation has become a requirement
But it’s not just the early adopters and pioneers;
as Industry 4.0 has matured and becomes mainstream, conservative and innovative organizations alike are embracing the journey of digital transformation.
According to Frost & Sullivan,
Digital transformation is not without challenges –
Executing successful, enterprise-scale digital transformation is more than just revamping older technologies –
Closed-loop models can deliver a 5 to 20% initial increase in productivity by reducing
planned and unplanned downtime, changeover time, speed losses, small stops, and scrap losses. This type of tangible impact allows manufacturing organizations to move from a largely reactive model to one that is fully integrative, predictive, sustainable, and adaptive.
Lack of resources and employee bandwidth,
shortage of technical expertise and domain knowledge, variability in manufacturing processes and digital maturity levels, issues with OT/IT networks integration and systems interoperability, and lack of user adoption due to technology diversity and a poor understanding of benefits are some of the reasons industrial companies fall into either pilot or scale purgatory.
Worker shortages:
Risk and cost pressures:
Digital disruption:
Timing
The lowest barrier to entry with digital transformation is finding efficiencies, driving productivity, and reducing costs. Many organizations are embracing a cost-first approach when it comes to digital transformation initiatives.
Reduced costs to improve efficiency:
Organizations are investing in areas with high growth and attainable market share. Initiatives include reducing time-to-market, introducing new products and business models, or increasing throughput.
Exponential growth through product innovation:
Becoming customer-centric is essential to staying ahead of your competition. To differentiate, companies are improving product quality, creating memorable customer experiences, and delivering heightened levels of service.
Heightened quality and customer engagement:
While the all-encompassing nature of digital transformation can feel overwhelming, it can also completely reinvent the way you run your organization and empower it to quickly adapt to new market conditions and customer needs. The successful implementation of digital transformation allows for:
Digital transformation – the act of enabling growth through digitalization – can seem like a daunting task.
01
Increased profits
02
Enhanced customer experience
03
Increased innovation
04
Improved agility
05
Better competitiveness
Gain a competitive advantage by prioritizing efficiency, cost reduction, sustainability, and overall innovation.
Better competitiveness:
Better competitiveness
05
Innovation acceleration and heightened flexibility lets you take control of your organization’s manufacturing procedures.
Improved agility:
Improved agility
04
Digital capabilities and connected solutions allow your assets to get to market faster.
Increased innovation:
03
Increased innovation
Improved quality and upgraded service procedures can create a seamless and efficient process.
Enhanced customer experience:
02
Enhanced customer experience
Organizations can maximize revenue by scaling to new markets and increasing throughput.
Increased profits:
Increased profits
01
Reduced costs to improve efficiency:
Exponential growth through product innovation:
Heightened quality and customer engagement:
Technology should not lead the transformation, which requires the support of people and processes to move forward. Instead, transformation and business goals should guide technology adoption and implementation.
3 of 3
Processes should be streamlined, simplified, and optimized.
2 of 3
People require new skills and ongoing training to perform their jobs better and experience a behavioral shift.
1 of 3
Reduced costs to improve efficiency:
Exponential growth through product innovation:
Reduced costs to improve efficiency:
Heightened quality and customer engagement:
Exponential growth through product innovation:
Heightened quality and customer engagement:
Transformation
What is Driving
Share this on social media
Share this on social media
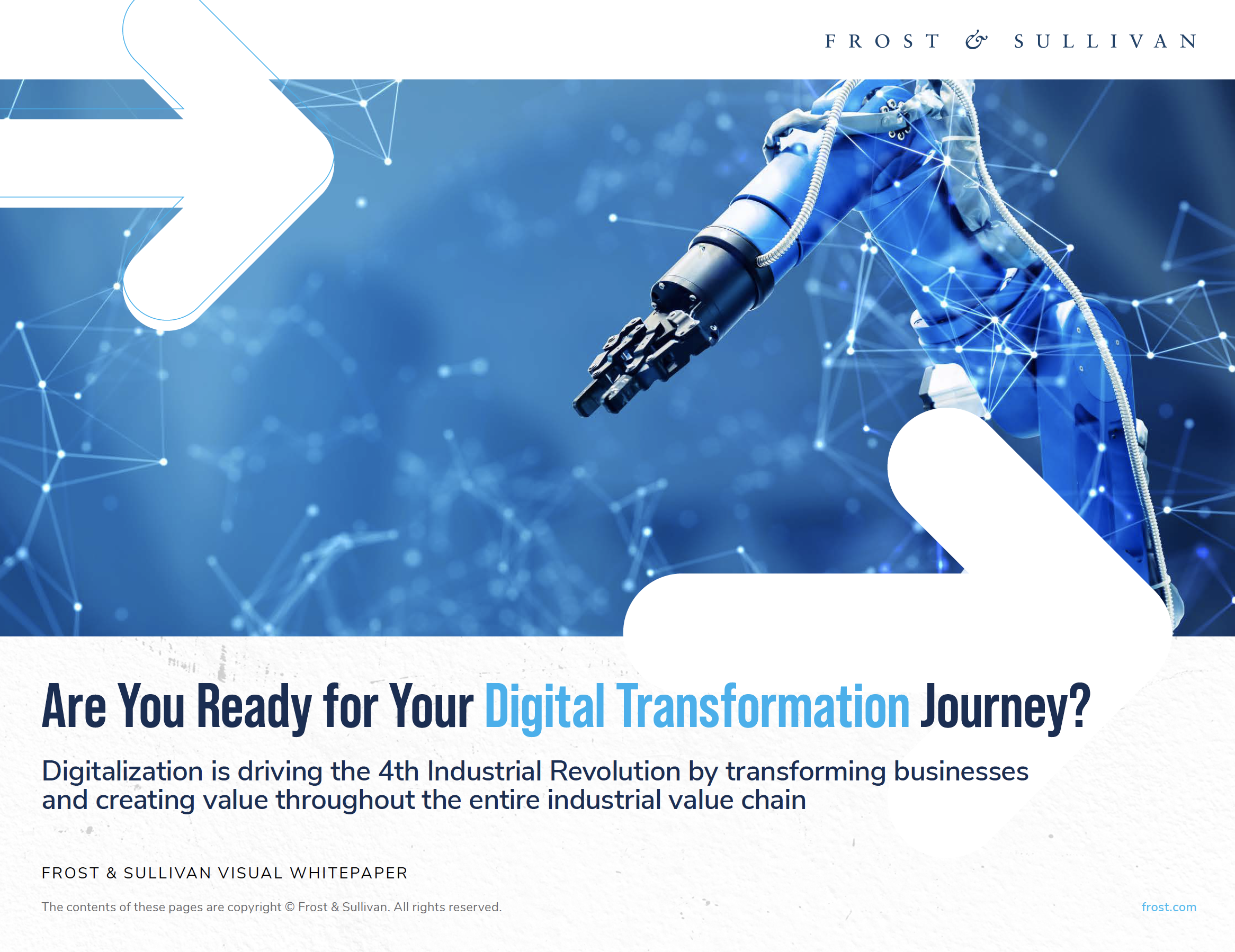