A Day in the Life of a Smart, Connected Worker
Meet John. John’s an Operator on a busy manufacturing plant floor. Throughout his day, he’s focused on meeting his customers’ demands for more tailored products and his bosses' demands for faster execution.
Luckily, John has the ThingWorx IoT platform. Let’s look at how John uses ThingWorx to get all the information he needs to do his work safely, efficiently, and up to spec.
Get Started

Starting His Day
Before ThingWorx
Now, John has work instructions that are connected to Engineering via a digital thread. They’re never out of date, because Engineering pushes changes to John without any latency. With just a click, John has an integrated view of:
Process plans and order of operations
Operation information
Tool information and control characteristics
Part Numbers
Warnings and safety precautions
Quality test instructions
Estimated operation completion time, and more
Using ThingWorx
John works off of assembly instructions from Engineering. But the static, paper-based instructions they provided were simply out of date as soon as they were printed. This led to scrap, rework, and time wasted searching for the right information, creating work-arounds, or waiting for an expert to help.
Predicting Maintenance and Preventing Downtime
Before ThingWorx
As he worked, John listened closely to his machines to constantly assess their status. After years with this equipment, he was an expert at noticing the tell-tale noises that meant something was out of whack.
Throughout his day, John can access his machines’ service history, along with their status and overall health—all in real-time. With just a glance at a screen, he can predict any needed maintenance—and use that data to prevent unnecessary downtime. John knows that he and his machines can work safely and efficiently, with no guesswork needed.
Using ThingWorx
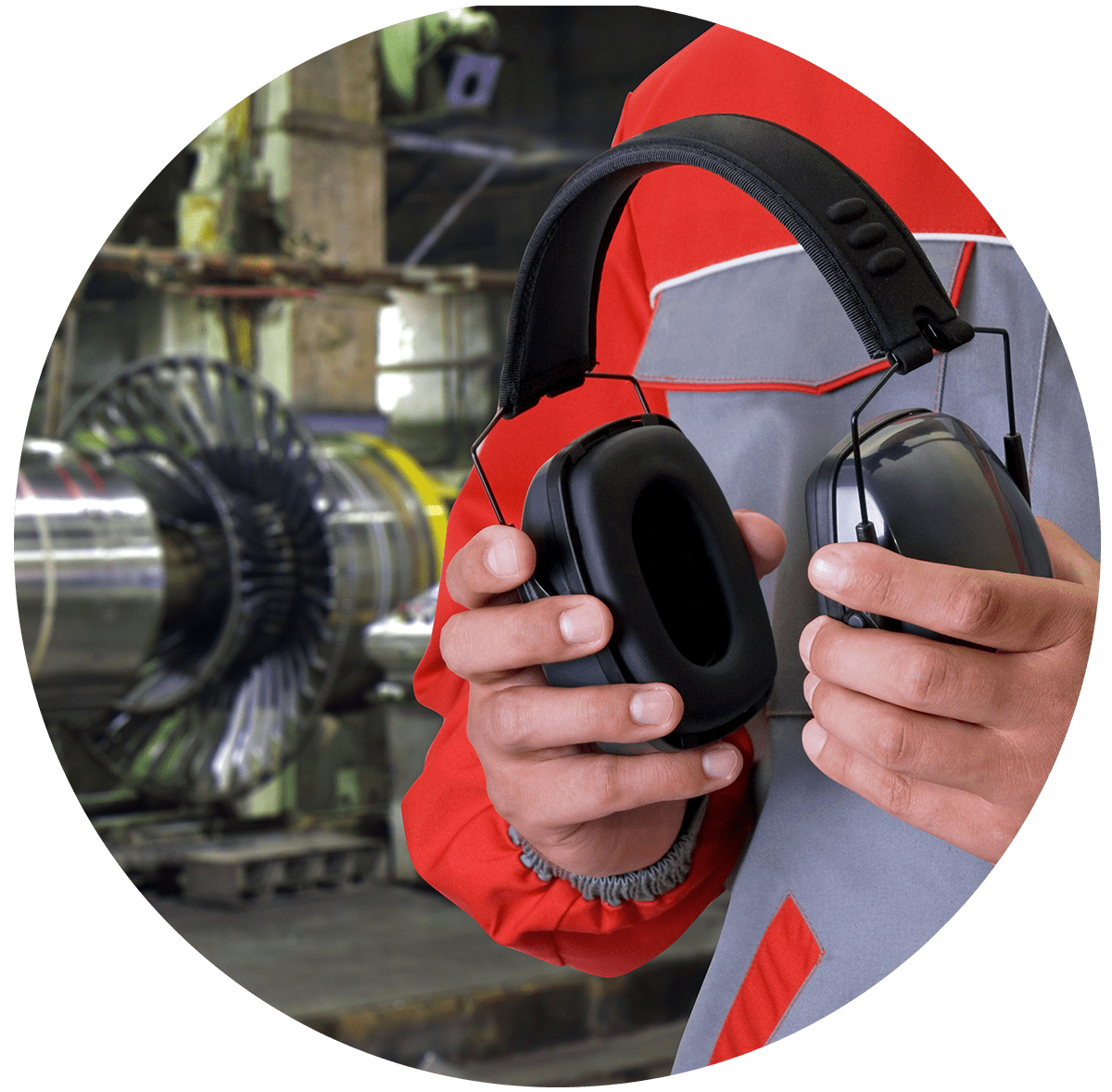
Calibrating Tools
Before ThingWorx
John used to spend time manually calibrating his tools each day, making sure they were set to the right specs based on the work instructions.
With smart tools connected to digital work instructions through ThingWorx, John's tools are automatically set to the correct, most up-to-date calibrations. Plus, all tool information is captured for product genealogy and traceability.
Using ThingWorx
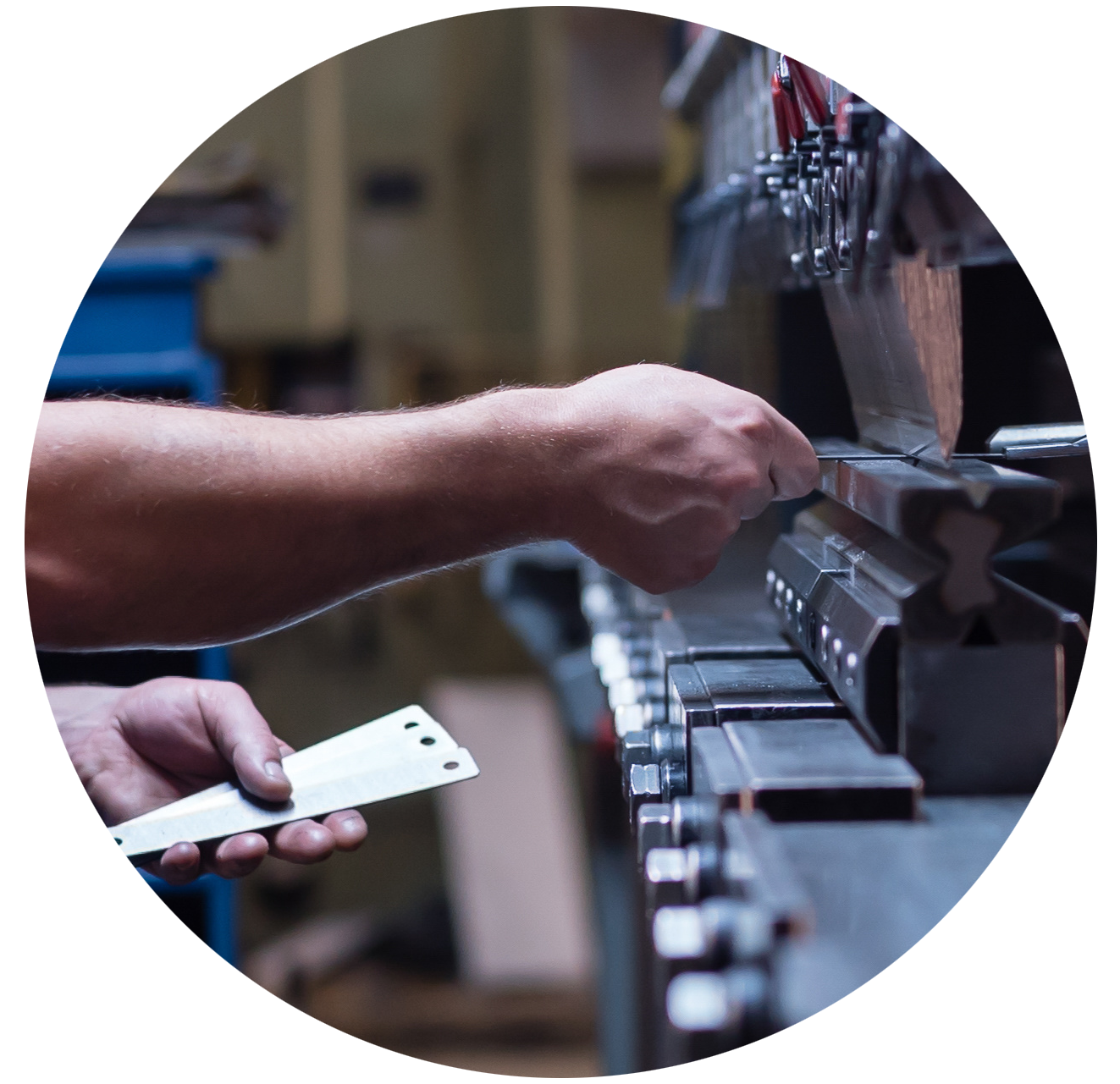
Capturing the Right Data
Before ThingWorx
After completing assembly, John wrote down all his important product data—including part serial numbers, number of parts consumed, how long it took to complete the work, etc.—on a piece of paper.
John inputs this vital data directly into the same interface as the digital work instructions, avoiding transcription errors, ensuring data integrity, and capturing historical part information.
Using ThingWorx
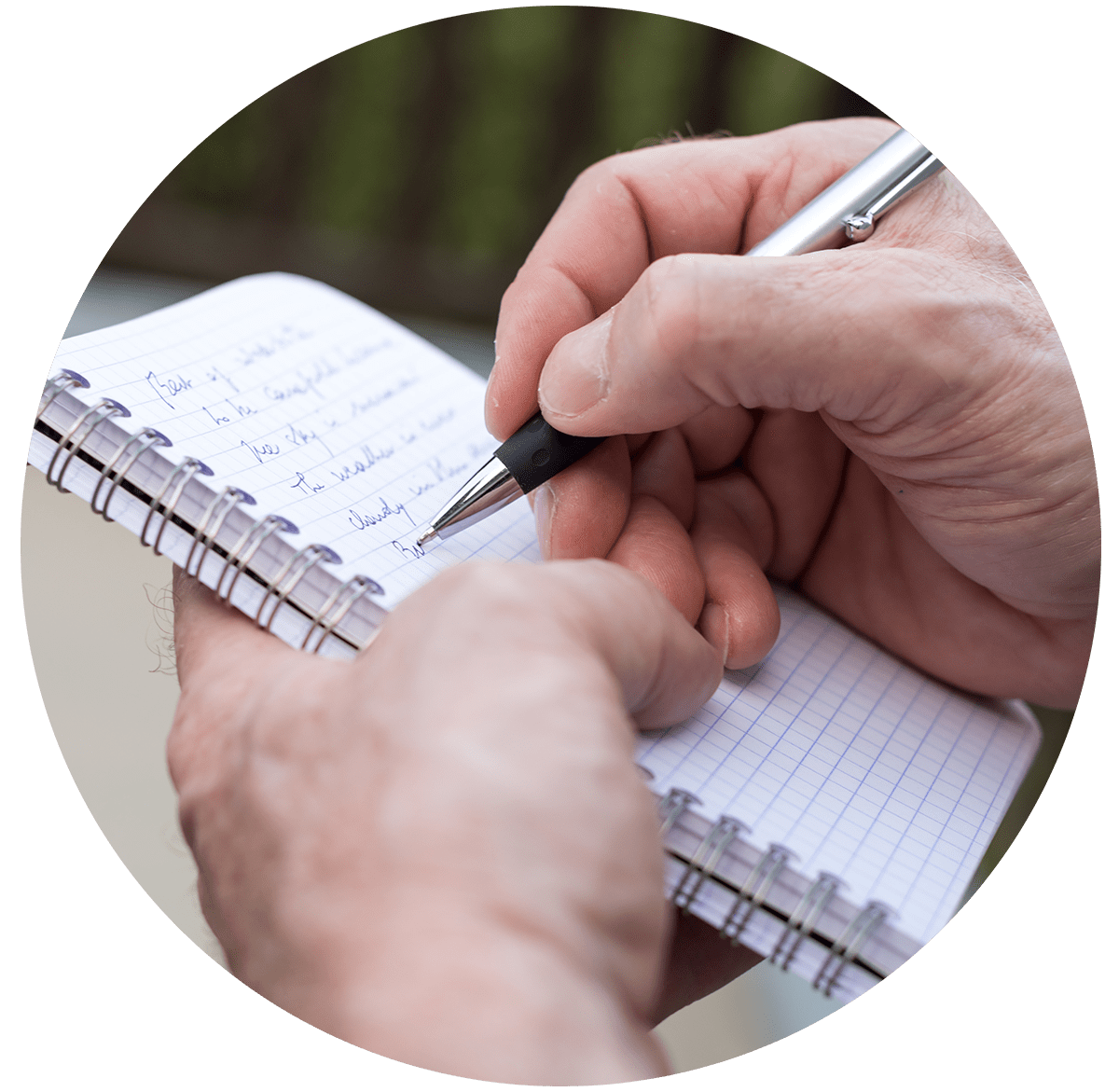
Passing Down to the Next Shift
Before ThingWorx
John used to end his days by waiting to talk to the next shift. Before he clocked out, he would walk them through work status, problems, machine health, and other important details of the day.
Now, all of John’s shift data is captured automatically throughout the day and is digitally shared with the next shift. John’s colleagues have the information they need to start their day, and John doesn’t need to wait to end his. John can focus on his final tasks, instead of worrying about prepping the next shift—and still know that every important pass-down item is captured.
Using ThingWorx
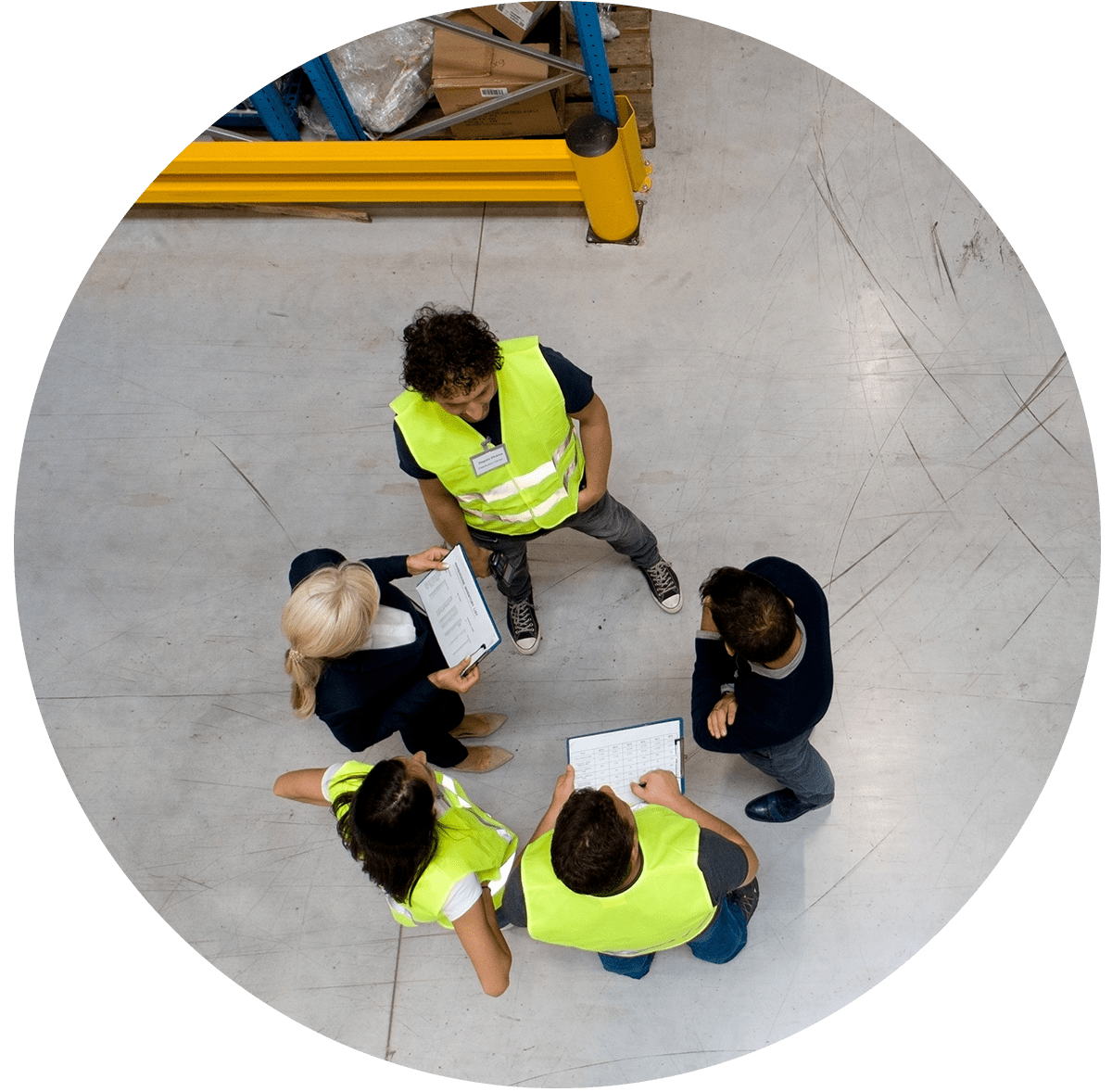
Want to make your operators’ days look more like John’s?
Learn More About Digital Work Instructions
