Avoiding Unplanned Downtime
Maximizing Labor Productivity
Predicting Maintenance Events
A Day in the New Normal:
Optimizing Throughput
Amidst the global COVID-19 pandemic, the notion of “business as usual” has taken on a different meaning, Manufacturers must manage ever-changing production volumes as their supply chains, customer demands, and workforce availability fluctuate. Whether contending with idled production or facing reduced–or record–demand, business at levels must adapt.
See how different roles across the enterprise can leverage the industrial Internet of Things (IIoT) to address throughput challenges in today’s “new normal,” and translate efficiency gains into a long-term competitive advantage.
Avoiding Unplanned Downtime
Predicting Maintenance Events
before
Between the traditional work instructions and manual processes for tracking data, Mary’s day-to-day relied on cumbersome pen and paper-based methods.
Without clear, up-to-date information, she encountered delays and product variations, which further complicated her shift handovers.
the new normal
Today, Mary’s safety and efficiency rely on having the right data at the right time. Digital work instructions provide an integrated view of simple, contextualized instructions—along with real-time process and product data.
Her shift data is also automatically captured, helping to facilitate an efficient, complete handover for the next operator.
Maximizing Labor Productivity
In the face of rapid-fire and unpredictable changes, IIoT solutions provide manufacturers with the visibility needed to address immediate throughput challenges and capture a competitive edge in the future.
With real-time data, predictive maintenance, and digital work instructions, your enterprise can pinpoint key optimization areas for today and increase flexibility to endure future, unknown conditions.
Planning to Thrive in the New Normal
and beyond
Maximizing Labor Productivity
before
As familiar as Mary was with her plant floor, she couldn’t identify process defects and hidden sources of waste until after the production cycle had finished. By that time, it was too late to prevent or remedy the issues that degraded product quality. The resulting needless scrap led to costly and timely rework.
the new normal
Today, Mary puts a stop to excess scrap by monitoring production performance in real-time. With real-time operational insights and alerts, she proactively detects and corrects inefficiencies, ensuring output is acceptable enough to satisfy customers and waste is minimized.
before
Without a way to know when or why an asset would fail, plant floor operator Mary could only react to machine outages after they occurred.
Unplanned downtime impeded Mary’s ability to stay on schedule and meet production deadlines. This reactive maintenance approach squandered time and resources, jeopardizing the ability to meet customer demands.
the new normal
Today, Mary needs the assets on her plant floor to be as efficient and reliable as possible, so staying ahead of potential failures is critical.
Using IIoT to gather real-time data and insights on past performance, Mary can proactively schedule maintenance without disrupting production—before a critical failure. With predictive maintenance, she can make data-driven decisions, based on machine status, to optimize efficiency.
before
While Mary worked to improve plant floor efficiency, her supervisor, Jamie, focused on macro-trends across multiple plants. But visibility was limited due to the disparate equipment, isolated processes, and complex systems that varied from plant-to-plant. The lack of clear data made it difficult for Jamie to drive improvements with confidence.
the new normal
Today, Jamie receives automated, real-time insights into performance macro-trends within the global enterprise. He even gets customized, real-time alerts so he can stay informed from any location. Using this data, he can remotely replicate high-performance processes across other lines and plants to better manage fluctuating demands.
Maximizing Labor Productivity
Monitoring Enterprise-Wide Performance Trends
before
the new normal
Today, in the face of pandemic-related absenteeism and worker redistribution, Jamie counts on digital work instructions to accelerate Mary’s upskilling and fast-track cross-training efforts for other operators. With a more flexible workforce, Jamie diminishes productivity-harming silos.
Maximizing Labor Productivity
Increasing Workforce Flexibility
Monitoring Enterprise-Wide Performance Trends
Increasing Workforce Flexibility
Jamie had long recognized Mary’s growth potential, making her a prime candidate for upskilling. But getting Mary work-ready on a different system required a lot of overhead and specialized training time.
Avoiding Unplanned Downtime
Maximizing Labor Productivity
Monitoring Enterprise-Wide Performance Trends
Increasing Workforce Flexibility
Predicting Maintenance Events
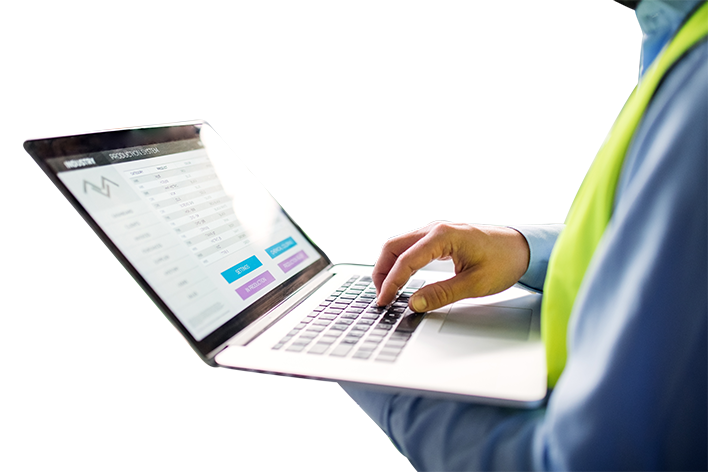