Facility assessment:
6 steps to more efficient warehouse operations
Shippers should always be looking for ways to optimize their network and save on resources, regardless of the state of the market. While carrier rates may be the most visible element of logistics costs, factors impacting warehousing operations—such as facility layout and design, storage space utilization, and picking and packing processes—can also eat into a business’ bottom line.
To remain competitive in a rapidly evolving industry landscape, shippers need to evaluate their warehouses and distribution centers on a regular basis to surface continuous cost and process improvement opportunities.
Conducting facility assessments is a great way for shippers to gauge their warehousing operations and performance. By diving deep into storage capacity, infrastructure, and technology, these assessments can help businesses hone in on areas of improvement to meet (and exceed) industry standards for safe, efficient, and compliant logistics operations.
Leverage assessment insights to make better decisions about your logistics strategies, minimize transportation risk, and enhance your supply chain efficiency.
Connect with an expert
Despite slowing demand in 2022...
Total logistics costs grew by
Inventory and carrying costs
increased by
1. Define the purpose and scope of the assessment.
The purpose and scope of a facility assessment can vary widely depending on the organization’s industry, size, and strategic priorities. For example, retailers may want to allocate more of their budget to improving their facility layout and inventory management, whereas food and beverage companies are more likely to be concerned with regulatory compliance around hygiene and safety. Ensure your assessment efforts are focused and aligned with your overarching business goals. This first step lays the groundwork for a successful evaluation, enabling leaders to set a realistic review timeline for cost and process improvements. The length of a given assessment will be determined by the facility’s square footage, availability of historic data and metrics, number of functional areas, types of equipment, and material ordering capabilities. For most thorough assessments, budget several months.
2. Gather the relevant documentation.
Start with detailed layout plans of the facility, including the arrangement of storage areas, aisles, workstations, and loading docks. If there are any previous facility assessments or audits, gather their reports. These documents provide insights into any existing process gaps and areas of improvement that may require further attention. Keeping customer expectations top of mind, make sure you have the right strategic framework and resources in place to effectively mitigate operational inefficiencies.
3. Create an end-to-end value stream map to identify process gaps within
and across functional areas.
Whether it’s packaging shipments or handling returned items, each functional area serves a unique purpose within the facility’s operations. Target the most important operational processes connecting each area, documenting their step-by-step workflows. Collect historical data on relevant KPIs such as order picking accuracy, cycle time, lead time, order fulfillment rate, and resource utilization. Review which digital tools are being leveraged for each process, including warehouse management systems (WMS) and automation.
4. Review performance metrics for root cause analysis.
Compare facility performance metrics against established benchmarks or industry best practices to pinpoint areas where numbers fall short or exceed expectations. Prioritize improvement opportunities within each functional area by determining which issues have the most significant impact on speed and cost, and which improvements can yield the most substantial benefits.
5. Communicate findings to relevant stakeholders.
Based on findings from the facility assessment, compile a detailed report outlining the current state of its functional areas. From process changes and technology upgrades to training initiatives and facility layout adjustments, make sure you provide data-driven recommendations for specific actions that address the identified challenges.
6. Develop a future roadmap for cost and performance improvement.
Create a report to communicate how your team’s suggested improvements would make a meaningful difference in facility operations. This report should provide a compelling roadmap that guides the implementation of improvements over time, with a structured timeline that breaks down project phases, target milestones, and tasks to be completed to achieve the desired objective. Don’t forget to specify the financial and technological resources required for each part of the improvement journey.
Facility assessment: The bottom line
By conducting a comprehensive facility assessment, facility leaders gain granular insights into how each of their functional areas are performing. From identifying new storage solutions to pinpointing potential hazards to eliminating unnecessary expenses, this analysis-driven approach can help shippers boost efficiency and save on resources.
What are you waiting for? Talk to an Uber Freight expert today to build a custom improvement plan for your logistics operations.
90.2%
19.6%
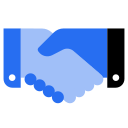