Case Study
Food product manufacturer saves $30M in freight costs using Uber Freight Control Tower and network services
Solution
Customer
Industry
Food Manufacturing
Size
130,000 employees
One of the largest food companies in the world, producing delectable goods and products from fruity confections to chocolate, pasta sauce, rice and also pet foods..
Customer profile
A global food product manufacturer was experiencing increased demand across a wide variety of products, creating logistics challenges and many points of inefficiency.
After operating for many years with a decentralized, warehouse-centric approach, the client realized that the organization needed far more real-time visibility into its logistics processes. They were pulling information from both payment provider tasks and third-party freight providers and it did not have a dashboard that provided a single source of truth for its logistics data. Instead, managers spent a significant amount of time on calls and sending emails with other team members to collect necessary information. Without a single view for the data insights they needed, leaders could not identify or proactively communicate and collaborate on transportation issues across various 3PLs.
Relying on the warehouse to manage logistics ultimately created high costs and unreliable delivery service, which hurt retailer satisfaction. But since they did not have reporting capabilities for transportation or financials, the organization was unable to determine how to mitigate these delays and higher-than-expected costs. Additionally, they were not able to measure carrier performance to make the best vendor decisions.
Opportunity: Optimize multi-product shipments to improve efficiency and cost-effectiveness
Opportunity
Talk to an expert today to find out how your business can benefit from one of the largest managed transportation and logistics networks with Uber Freight.
Connect with an expert
Partnering with Uber Freight enabled the food product manufacturer to provide the same care and attention to its products as the loyal customers who buy them. They credit their success with new logistics initiatives not only to Uber Freight’s technology, but the collaborative approach of the project.
By gaining real-time data visibility from Uber Freight’s Control Tower and strategic supply chain insights from the VIP, the company achieved over $30 million in savings. Additionally, they increased their on-time service to 90% on low-volume lane shipments. And to help their core value of sustainability, the organization also reduced greenhouse gas emissions by 12,000 metric tons (7%). Moving from disparate and manual warehouse operations to an optimized, single source of visibility with Uber Freight helped the company modernize and optimize their shipping processes for more happy retailers and customers alike.
Results: Massive cost savings, greener operations, and more on-time shipments
Results
The company began collaborating with Uber Freight to gain true visibility into its entire network and benchmark performance against other CPG companies. Immediately after deploying Uber Freight’s Control Tower and network services, they were able to establish a single view for data insights and implement real-time tracking.
With the new system, managers could see how many days of lead time were allocated and proactively make changes if they could foresee delays. The team also quickly realized that the delivery delays were largely due to issues with coding. In one example, Uber Freight used its optimization engine to create custom, automated codes for consolidating various products together to optimize shipping efficiency and cost. Uber Freight’s Optimization Engine then generated codes that dictated when its gum and mint products could be shipped with chocolate, or when these products exceed the threshold to ride together based on several variables. This type of planning and optimization had to be done manually in the past by managers.
With the new visibility into its network, they can make more strategic decisions to address its transportation issues, leveraging an array of Uber Freight services to improve shipping collaboration, performance and cost. For example, Uber Freight's OptiPro provided new insights into all underutilized truckload shipments, unearthing new opportunities to convert several long-haul truckload (LTL) lanes to rail. The tech also enabled new cross-collaboration within other Uber Freight CPG customer networks to consolidate shipments, closing loops and keeping drivers moving. In another instance, after identifying carrier performance as a key issue, the company worked with Uber Freight to implement carrier performance management and a spot market control (FAM) process.
They also identified and implemented several opportunities to drive strategic supply chain improvements through collaboration with Uber Freight's Value Improvement Program (VIP).
Lastly, with Uber Freight’s Dock Scheduling tool, the company was able to improve order flow issues that had previously caused site shutdowns and delays on a regular basis. The new tool allows them to space shipments more evenly, preventing the team from becoming overloaded and experiencing delays.
Solution: A high-level of data visibility with Uber Freight’s Control Tower
“...BASF was able to gather and analyze data to better understand how its business compares to others within the chemical industry and throughout the entire Uber Freight network.“
By gaining real-time data visibility from Uber Freight’s Control Tower and strategic supply chain insights from the VIP, the company achieved over $30 million in savings and increased their on-time service to 90%.
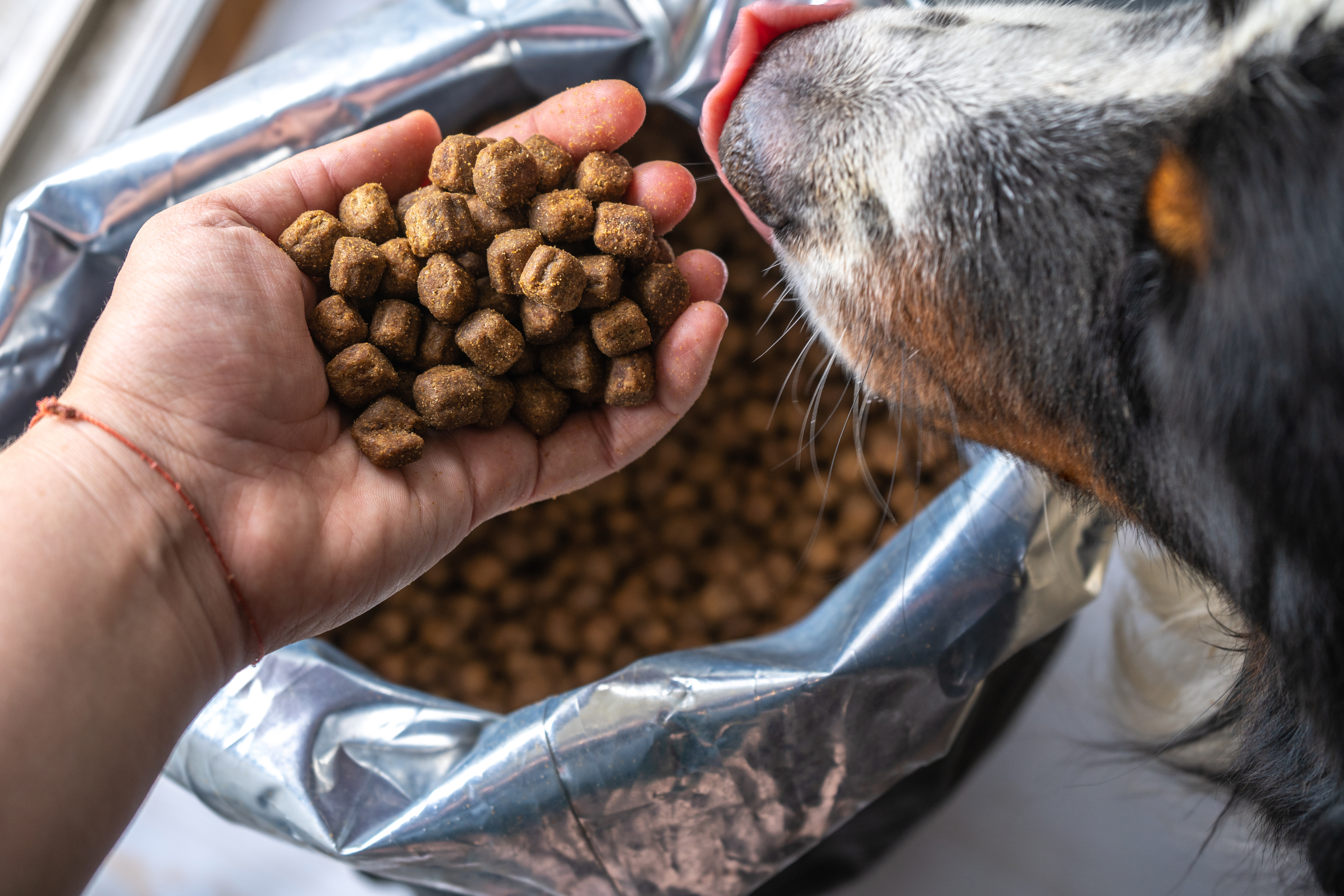