Misconception Versus Fact:
Lithium-Ion UPS Battery Recycling
This infographic debunks some of the common
misconceptions surrounding the recycling of
Lithium-ion batteries in UPS systems.
Uninterruptible power supply (UPS) systems with lithium-Ion (Li-ion) batteries have become popular in the data center for their industry-leading power protection for critical equipment in core and edge applications. Compared to valve regulated lead–acid (VRLA) batteries, Li-ion batteries last 2-3 times longer, and their smaller size and lighter weight save space and increase the flexibility of where a UPS can be deployed. Despite the benefits of the technology, there’s a great amount of skepticism regarding the costs and viability of recycling Li-ion batteries. Below are some of the common myths surrounding Li-ion and why these myths are merely misconceptions.
Vertiv™ Liebert®
GXT5 Lithium-Ion
UPS 5000 - 10000 VA,
120V/208V
Vertiv™ Liebert®
GXT5 Lithium-Ion
UPS 1000 - 3000 VA, 120V
Vertiv™ HPL
Lithium-Ion Battery
Below are the list of misconceptions, and to debunk them, press the icons in the middle to see real facts.
FACT
MISCONCEPTION
This was likely the case several years ago, but more recycling companies today are using recycling processes that recover more of the valuable elements in the battery while minimizing or eliminating waste byproducts. These companies provide a viable option for recycling Li-ion batteries sustainably and, in some cases, the value of the salvaged elements found in the batteries can offset the overall costs of the recycling process.
Most lithium-ion UPS batteries
just end up in a landfill.
Today’s recycling processes for Li-ion batteries are becoming increasingly adept at recovering more of the battery’s most valuable materials, such as cobalt, nickel, lithium and manganese. A chemical process known as hydrometallurgy uses aqueous solutions to separate metals from the “black mass” of crushed battery modules and recover up to 98% of the battery’s elements. Through chemical separation, the materials reach the purity level of battery-grade materials and can be used to create new batteries.
The process of recycling
a lithium-ion battery is inefficient.
The value of materials recovered in Li-ion batteries can help offset the overall costs related to recycling and transportation. Further, some valuable metals in these batteries are sourced from areas where mining companies are being accused of exploiting workers and destroying local habitats. As a result, manufacturers are turning to “urban mining” using recycled metals instead of those extracted from the earth. The more valuable materials that can be salvaged, the more money to be made by selling it back to the supply chain.
Recycling lithium-Ion batteries
is not worth the costs.
As demand for Li-ion batteries grows, several manufacturers working to lessen dependency on mining for precious metals have garnered serious attention over the last few years. In North America, Li-Cycle, a company that recovers Li-ion materials and reintroduces them back into the supply chain, made its debut as a public company in 2021. Last year, Ascend Elements, a manufacturer of advanced battery materials using valuable elements reclaimed from spent lithium-ion batteries, secured more than $780 million in funding to assist with the commercialization of
its closed-loop process.
Recycling lithium-Ion batteries
is not worth the costs.
To learn more about Li-ion battery recycling and the major players helping to make the process more convenient, profitable and sustainable, download our white paper.
FACT
MISCONCEPTION
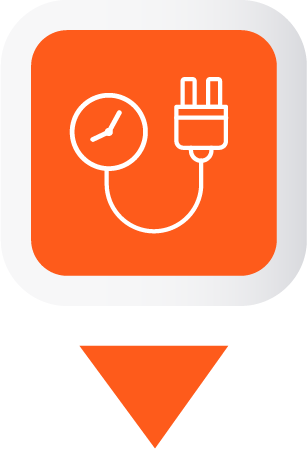